News and Views, Volume 54 | Materials Lab Featured Damage Mechanism
STRAIN-INDUCED PRECIPITATION HARDENING (SIPH) IN AUSTENITIC STAINLESS BOILER TUBES
By: Wendy Weiss
Structural Integrity’s Metallurgical Laboratory offers comprehensive metallurgical laboratory services to support client material issues.
Strain-Induced Precipitation Hardening, also known as SIPH, is a commonly misinterpreted boiler tube failure mechanism that occurs when austenitic stainless steel tubing is cold or warm worked during fabrication and then is installed with either improper or no solution annealing heat treatment. While the basic mechanism and the root cause are understood, the complex interaction between heat chemistry, quantity of cold or warm work, and subsequent thermal history makes it very difficult to predict under precisely what circumstances damage due to SIPH will result in failure of a boiler tube.
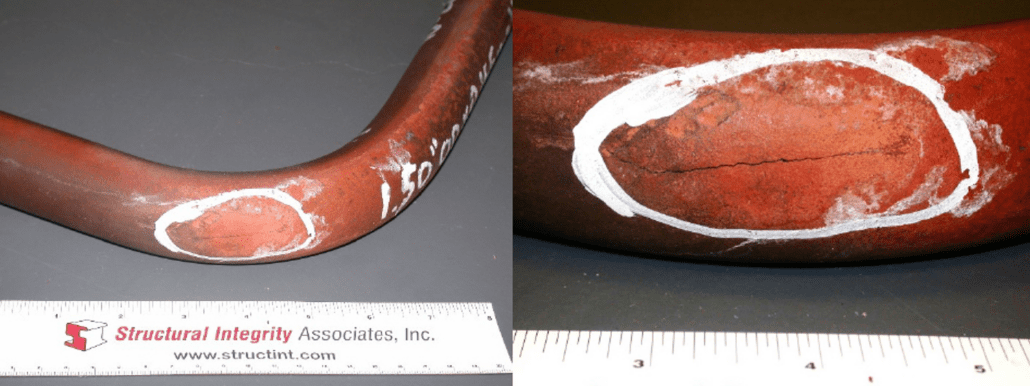
Longitudinally oriented crack at the extrados of a bend in a stainless steel superheater tube.
Mechanism
SIPH occurs when a heat of austenitic stainless steel containing certain precipitate-forming elements (e.g., niobium, titanium, vanadium, etc.) either intentionally or as residuals is cold or warm worked during subsequent material processing. The cold or warm working creates excess defects in the sub-structure of the material, which serve as preferred sites for precipitation of temper-resistant carbides or carbo-nitrides. Precipitation occurs when the material is heated to a sufficiently high temperature that is well below the solution annealing temperature. This can occur rapidly during a poorly executed heat treatment if the material does not reach the proper solution annealing temperature, or it can occur more slowly at typical operating temperatures for superheater or reheater tubing in utility-type boilers.
Once formed, precipitates anchor to the defects, resulting in a substantial increase in the elevated temperature or creep strength of the interior of the grains. At the same time, there is a narrow zone of material immediately adjoining the grain boundaries that remains largely precipitate-free due to the diffusional characteristics of the grain boundary itself. Ultimately, the interior portion of the individual grains becomes very strong at elevated temperatures while the material immediately adjoining the grain boundaries becomes comparatively creep weak. In addition, any surface-active elements that may be present in the material, such as arsenic, tin, antimony, etc., will tend to concentrate at the grain boundaries, further reducing their strength.
Regardless of when the precipitation occurs, once the interior of the grains has been strengthened, the grain boundary regions are weakened. Any strain imposed on the material in response to an applied or residual stress is forced to concentrate in the grain boundary region, which substantially magnifies its effect. For example, suppose the bulk strain experienced by a cold-worked stainless superheater tube segment is very small – a fraction of a percent – and the material has undergone the SIPH reaction. The strengthened grain interiors will undergo no strain. Conversely, within the much smaller volume of the comparatively weak grain boundaries, the accumulated strain will be orders of magnitude higher than the bulk level.
Typical Locations
- Bends
- Offsets
- Swages
- Welded attachments
Features
- Can initiate at midwall
- Early-stage damage consists largely of grain boundary cavities and microfissures
- Intergranular cracking
Root Causes
The single root cause of SIPH is the failure to properly solution anneal susceptible heats of austenitic stainless steel tubing that has been either cold or warm worked during fabrication.
An overall, cross-sectional view of the intergranular crack (image A) with higher magnification views of some of the secondary grain boundary microfissures and voids (image C). Slip bands (parallel lines in image B) indicate local deformation.
For any situation involving material property characterization, Structural Integrity has an experienced group of materials specialists and a full-service metallurgical testing laboratory that can help.
Visit Our Metallurgical Laboratory Services Page
SEE THESE OTHER RELATED MATERIALS FROM THE SIA METALLURGICAL LABORATORY